1. 材料选择依据
黑碳化硅的特性使其成为马蹄磨块的理想选择:
- 高硬度与耐磨性:莫氏硬度达 9.5 级,仅次于金刚石,能有效切削石材表面并保持自身耐用性,减少磨块更换频率
- 韧性优势:相较于绿碳化硅,黑碳化硅韧性更高,适合加工大理石、花岗岩等脆性石材,不易在研磨过程中崩裂
- 成本效益:黑碳化硅的生产成本低于绿碳化硅,且能满足石材研磨的常规需求,性价比更高
2. 行业应用实例
- 产品规格:例如中星厂生产的法兰克福马蹄型抛光磨块明确标注材质为黑碳化硅,粒度通常为 600 目左右,适用于大理石抛光的最后一道工序
- 配方设计:传统菱苦土结合的马蹄磨块中,黑碳化硅作为主要磨料,与氧化镁、氯化镁等结合剂混合,形成高锋利度和耐磨性的磨具
- 粒度范围:根据研磨阶段不同,黑碳化硅粒度可覆盖 24# 至 2500#,例如粗磨阶段常用 36#-80#,精磨阶段则使用 800#-2500#
3. 工艺与性能表现
- 结合剂类型:黑碳化硅磨块可采用树脂、金属或菱苦土结合剂。例如,树脂结合的黑碳化硅磨块兼具耐磨性和抛光效果,而菱苦土结合的磨块则以高锋利度著称1516。
- 应用场景:马蹄磨块常用于石材的粗磨、中磨和精磨,尤其在大理石、石英石等板材的抛光工序中,黑碳化硅能快速去除表面划痕并提升光泽度
4. 替代材料对比
- 绿碳化硅:虽硬度更高(纯度 > 97%),但自锐性强、成本高,主要用于硬质合金或光学玻璃加工,较少用于石材研磨
- 金刚石:虽耐磨性优异,但成本高昂,通常用于高端或特殊需求的磨块(如金属结合剂金刚石磨块),而黑碳化硅仍是主流选择
5. 行业标准与制造规范
- 粒度分级:根据 GB/T 2480-2022 标准,黑碳化硅粒度范围覆盖 20# 至 2500#,需通过精密筛分确保颗粒均匀性,以保证研磨效果一致性
- 结合剂配比:例如树脂结合剂的黑碳化硅磨块,其配方通常包含 35-60% 树脂、5-25% 磨料(黑碳化硅)及填料,通过热压或常温固化成型
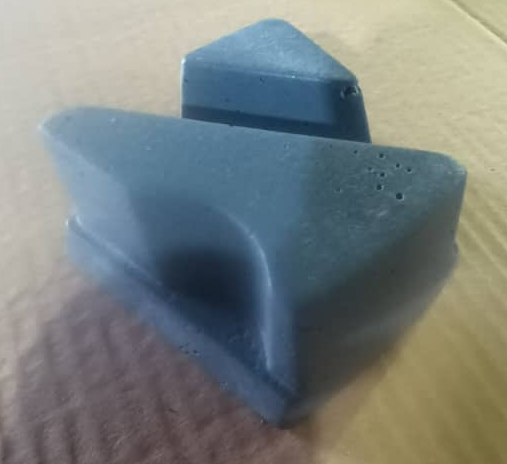